martes, 21 de noviembre de 2017
lunes, 20 de noviembre de 2017
LOS RESIDUOS
En zonas urbanas con actividades muy diversificadas se producen diferentes tipos de residuos como los domesticos, industriales, asimilables a urbanos, de construccion y objetos de gran tamaños( electrodomesticos, muebles...)
En cuanto al tratamiento se distinguen los siguientes:
Vertederos controlados: los residuos se depositan en celulas y se cubren con tierras formando capas. Una vez lleno el vertedero se cubre de tierra vegetal.

Incineración: consiste en quemar los residuos. Su principal problema es la formación de residuos gaseosos.
Producción de metano: La descomposición natural de la materia organica produce un gas, rico en metano y dioxido de carbono, que se utiliza en la red de gas ciudad o bien se quema para producir energía electrica.
Compostaje: la materia organica se titula con objeto de eliminar la mayor cantidad de agua posible. El resultado es una especie de humus que sirve de abono.
Reciclados de materiales: La decison de recuperar materiales regenerables esta en función de los gastos economicos que se pueden realizar. Actualmente existen metodos tecnologicos para separar papel, vidrio, hierro y otros materiales no ferricos.
El mayor problema de la recuperacion consiste en la separación de los materiales. Se puede realizar en origen (mediante contenedores especializados) o en plantas diseñadas para ello. La separacion presenta muchos problemas y es muy cara.
En cuanto al tratamiento se distinguen los siguientes:
Vertederos controlados: los residuos se depositan en celulas y se cubren con tierras formando capas. Una vez lleno el vertedero se cubre de tierra vegetal.

Incineración: consiste en quemar los residuos. Su principal problema es la formación de residuos gaseosos.
Producción de metano: La descomposición natural de la materia organica produce un gas, rico en metano y dioxido de carbono, que se utiliza en la red de gas ciudad o bien se quema para producir energía electrica.
Compostaje: la materia organica se titula con objeto de eliminar la mayor cantidad de agua posible. El resultado es una especie de humus que sirve de abono.
Reciclados de materiales: La decison de recuperar materiales regenerables esta en función de los gastos economicos que se pueden realizar. Actualmente existen metodos tecnologicos para separar papel, vidrio, hierro y otros materiales no ferricos.
El mayor problema de la recuperacion consiste en la separación de los materiales. Se puede realizar en origen (mediante contenedores especializados) o en plantas diseñadas para ello. La separacion presenta muchos problemas y es muy cara.
EL TITANIO Y SUS ALEACIONES
Son materiales de utilizacion muy reciente, que presentan una serie de propiedades de muy buena combinación. El titanio puro tiene una densidad baja y un punto de fusión muy elevado. Estas aleaciones poseen una extremada resistencia, son muy dúctiles y facilmente forjables.
El principal inconveniente del titanio es su alto poder de reacción con otros materiales a altas temperaturas. Debido a esta limitación se hace necesario el diseño de tecnicas de moldeo y afines para obtener este tipo de aleaciones. A pesar de todo, la resistencia a la corrosión es muy elevada, y tienen un buen comportamiento frente a ambientes marinos, atmosfericos, y muchos productos industriales.
El principal inconveniente del titanio es su alto poder de reacción con otros materiales a altas temperaturas. Debido a esta limitación se hace necesario el diseño de tecnicas de moldeo y afines para obtener este tipo de aleaciones. A pesar de todo, la resistencia a la corrosión es muy elevada, y tienen un buen comportamiento frente a ambientes marinos, atmosfericos, y muchos productos industriales.
jueves, 16 de noviembre de 2017
EL MAGNESIO Y SUS ALEACIONES
La característica más relevante es su densidad, por tanto se utilizan por su bajo peso. El magnesio tiene una estructura cristalina HC, relativamente blanda. A temperatura ambiente el magnesio y sus aleaciones se deforman con dificultad debido a la estructura cristalina. Quimicamente, las aleaciones de magnesio son inestables y susceptibles a la corrosión marina. pero son relativamente resistentes a la corrosión atmosférica.El magnesio además de tener como desventaja frente al aluminio el precio, presenta el inconveniente de que en estado líquido arde en contacto con el aire.
Las aleaciones de magnesio se clasifican en moldeables y forjables, algunas se pueden tratar térmicamente. Los elementos más comunes son aluminio, cinc y manganeso.


EL ALUMINIO Y SUS ALEACIONES
Tanto el aluminio como sus aleaciones se caracterizan por la relativa baja densidad, las elevadas conductividades eléctricas y térmicas, y la resistencia a la corrosión. Por su elevada ductilidad, se puede trabajar con facilidad hasta convertirlo en papel. Su principal limitación es la baja temperatura de fusión.
El aumento de la resistencia mecánica del aluminio se consigue por acrietud y por aleación. No obstante, ambos procesos disminuyen su resistencia a la corrosión. Los elementos mas comunes en la aleación de aluminio son cobre, magneso, sicilio y cinc. Las aleaciones se suelen clasificar en aleaciones para moldeo y aleaciones para forja.
El aumento de la resistencia mecánica del aluminio se consigue por acrietud y por aleación. No obstante, ambos procesos disminuyen su resistencia a la corrosión. Los elementos mas comunes en la aleación de aluminio son cobre, magneso, sicilio y cinc. Las aleaciones se suelen clasificar en aleaciones para moldeo y aleaciones para forja.

jueves, 9 de noviembre de 2017
EL COBRE Y SUS ALEACIONES
El cobre sin alear es tan blando y ductil que es dificil de mecanizar, pero tiene una buena capacidad para ser trabajado en frio. Resiste muy bien a la corrosión. La resistencia mecanica y el comportamiento ante la corrosión del cobre mejoran con su aleación. La mayoría de las aleaciones no se endurezen con tratamientos térmicos, pero esta propiedad se mejora mediante acritud y formacion de disoluciones sólidas.
La aleación más común del cobre es el latón, donde el cinc se considera el soluto y principal componenten de la aleación. Los bronces son aleaciones de cobre con estaño, que también puede contener aluminio, sicilio y níquel; son más resistentes que los latones y tienen gran resistencia a la corrosión. Se emplean cuando se requiere una elevada resistencia a la corrosión y buena resistencia a la tracción, así como a desgaste, por lo que son muy apreciados para cojinetes y engranajes.
Riopar Viejo y la Fabrica de Bronce
La Reales fábricas de bronce y latón de San Juan de Riópar (Albacete) fueron creadas en 1773 por el ingeniero vienés nacionalizado español Juan Jorge Graubner, atraído por la noticia de la existencia de una mina de calamina, mineral del que se extrae cinc para fundirlo con cobre y crear la aleación llamada latón, y su actividad industrial se prolongó durante 156 años.
Al estar encaramado sobre una roca, lo que le da unas vistas impresionantes, no pudo seguir expandiéndose. Por esto, y coincidiendo con la fundación de la Real Fábrica de Bronce de San Juan de Alcaraz en el siglo XVIII, se creó el pueblo de Riópar a unos 6 kilómetros.
La Real Fábrica de Bronce, que data del siglo XVIII y que fue la primera de España y segunda del mundo. La ubicación de una fábrica de este tipo en esta zona era perfecta por varios motivos. Aquí había minas de calamina, de donde se extrae el zinc. Y además hay agua y madera, dos elementos fundamentales para poner en funcionamiento las fábricas. En total había 8 y cada una se encargaba de una parte del proceso de fabricación del bronce. En ellas se elaboraba latón (aleación de cobre + zinc) y bronce (cobre + estaño). El cobre se traía de fuera.

A pesar de que nunca fue rentable económicamente, siempre estuvo abierta. Incluso durante la Guerra Civil, aunque les obligasen a fabricar bombas. A lo largo de los años, Riópar ha tenido varios nombres: Reales Fábricas de San Juan de Alcaraz, Fábricas de San Juan de Alcaraz, Fábricas de Riópar y, finalmente, Riópar. Por ello, es bastante común que la gente siga refiriéndose a este pueblo como Fábricas. Toda esta evolución nominal tiene sentido, ya que Riópar existe gracias a esta industria.

ALEACIONES NO FÉRRICAS
Los productos siderúrgicos tienen como principales defectos:
- una densidad relativamente elevada.
- conductividad eléctrica comparativamente baja.
- sensibles a la corrosión y oxidacion atmosférica.
Altos hornos en España
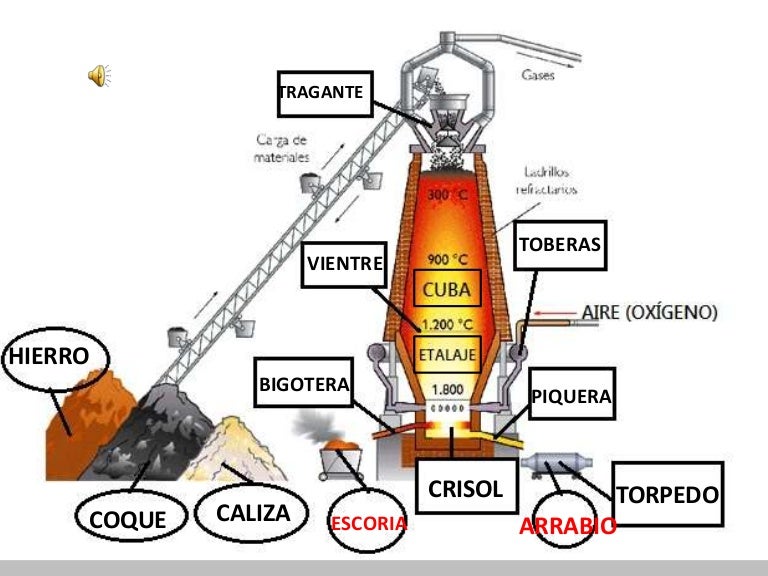
"El PIB industrial español ha ido ganando posiciones con respecto al de los países avanzados de Europa (salvo en 1950, una fecha inserta dentro de la posguerra civil), sin llegar a alcanzarlo nunca (inferior al 30% en 1950, cercano al 80% en 1996)". Este ascenso, más rápido que el de los países industrializados de Europa, debido a la extrema debilidad del punto de partida, "expresa al mismo tiempo el mérito y la insuficiencia del progreso industrial” de España.
La industria siderúrgica española ha experimentado poco más o menos, las mismas vicisitudes. Atraso técnico, combustible caro o de mala calidad y un mercado de dimensiones reducidas hicieron que la siderurgia española, a lo largo del siglo XIX, no pudiera competir con productos ingleses, belgas o alemanes.
La industria siderúrgica española ha experimentado poco más o menos, las mismas vicisitudes. Atraso técnico, combustible caro o de mala calidad y un mercado de dimensiones reducidas hicieron que la siderurgia española, a lo largo del siglo XIX, no pudiera competir con productos ingleses, belgas o alemanes.

Más tarde, la siderurgia pasó a Andalucía. Siguiendo el modelo europeo de altos hornos al carbón vegetal y afinación y laminación a la hulla se instalaron plantas en Marbella (Málaga) y en Cazalla de la Sierra (Sevilla).
Pero la hegemonía de la siderurgia andaluza no pudo prolongarse más allá de 1863, “Cuando las fábricas asturianas de Mieres (desde 1852) y La Felguera (desde 1.859) empezaron a trabajar a pleno rendimiento.
La primacía de Asturias se debió a la abundancia de hulla y de mena de hierro en su territorio. Pero esta primacía, después de la irrupción del convertidor Bessermer, pasó a Vizcaya. Al terminar en 1876 la Segunda Guerra Carlista, algunos empresarios europeos con el fin de conseguir mineral barato para sus altos hornos, comenzaron a instalarse en la ría del Nervión. La oferta aparecía así dividida entre los productores asturianos y vascos. Empezó una gradual sustitución de los convertidores Bessemer por otros sistemas de fabricación, difundidos en Europa y EEUU. Apareció así el "horno abierto" Martin-Siemens que mejoraba el método del Bessemer.
Se acentuó la hegemonía vizcaína al frente de la siderurgia española y se concentró toda la producción en el norte. En la época de la Gran Guerra, el primer productor siderúrgico de España era Vizcaya, seguida de Asturias y después Santander, Alava, Guipúzcoa y Navarra.
Se acentuó la hegemonía vizcaína al frente de la siderurgia española y se concentró toda la producción en el norte. En la época de la Gran Guerra, el primer productor siderúrgico de España era Vizcaya, seguida de Asturias y después Santander, Alava, Guipúzcoa y Navarra.

Después de la Primera Guerra Mundial, a las provincias cantábricas se añadieron dos nuevas competidoras, Barcelona y sobre todo Valencia, que en los años 20 superó a Asturias.
Después con el franquismo, se creó Ensidesa, que dio lugar a Aceralia, que se integró con la francesa Usinor y la luxemburguesa Arbed, creando así la actual Arcelor.
Después con el franquismo, se creó Ensidesa, que dio lugar a Aceralia, que se integró con la francesa Usinor y la luxemburguesa Arbed, creando así la actual Arcelor.
lunes, 6 de noviembre de 2017
Diagrama Hierro-Carbono
En el diagrama de equilibrio o diagrama de fases hierro-carbono (Fe-C) (también diagrama hierro-carbono), se representan las transformaciones que sufren los aceros al carbono con la temperatura, admitiendo que el calentamiento (o enfriamiento) de la mezcla se realiza muy lentamente, de modo tal que los procesos de difusión (homogeneización) tengan tiempo para completarse. Dicho diagrama se obtiene experimentalmente identificando los puntos críticos, temperaturas a las que se producen las sucesivas transformaciones por diversos métodos.


Zona de los aceros (hasta un 2 % de carbono) del diagrama de equilibrio metaestable hierro-carbono. Dado que, en los aceros, el carbono se encuentra formando carburo de hierro, se han incluido, en abscisas, las escalas de los porcentajes en peso de carbono y de carburo de hierro (en azul).
En la siguiente imagen podemos ver el mismo diagrama, con un mayor contraste para facilitar su comprension:
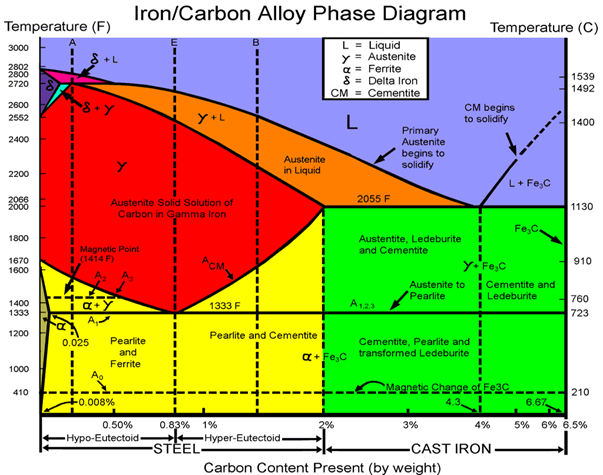
Y este diagrama es el que estudiamos en 1º de bachiller:


Suscribirse a:
Entradas (Atom)
Memoria proyecto
Memoria proyecto tecnologia de Juan Torrijos Torres
-
El funcionamiento del tren bala se basa en la leviacion magnetica mediante la utilizacion de superconductores. Hay dos tipos de supercondu...
-
El Efecto Meissner- Ochsenfeld fue descubierto por Walther Meissner y Robert Ochsenfeld en 1933, y consiste en que cuando un superconduct...